Cross-Docking: Definition, Benefits, Challenges, and More
As flu season approaches, pharmaceutical manufacturers and distribution centers must prepare for the surge in demand for vaccines and other medical supplies. With many of these products, especially vaccines, being temperature-sensitive, it’s crucial to ensure they don’t spoil while waiting in storage or non-climate-controlled environments. Efficient logistics, such as cross-docking, can play a vital role in maintaining the quality and speed of distribution for these perishable goods.
Cross-docking is a logistics strategy that minimizes the time products spend in transit and storage, helping products like flu vaccines move from manufacturers to the end customer swiftly, while preserving ideal storage conditions.
Even if you don’t work in pharmaceuticals, you may be wondering, “What does this mean for my business?” Let’s dive into what cross-docking is, its various types, how it works, its benefits, and its potential challenges—especially for third-party logistics (3PL) and eCommerce fulfillment.
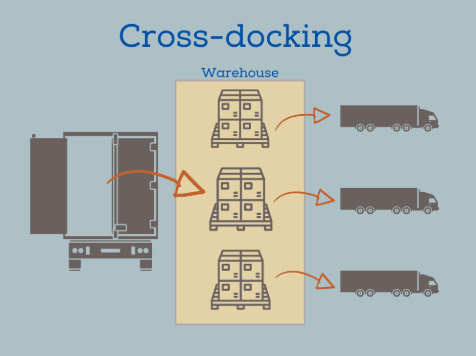
Cross-docking is a logistics practice where inbound goods are transferred directly from receiving to shipping with minimal storage time. This practice reduces transportation and handling costs, accelerates inventory turnover, and streamlines supply chain management.
In traditional warehousing, products are stored for an extended period. In contrast, cross-docking warehouses immediately sort products upon arrival at the receiving dock and load them directly onto outbound trucks, ensuring rapid delivery.
There are three main types of cross-docking:
- Manufacturing Cross-Docking: Products required for manufacturing are received and prepared for production without long storage periods.
- Pre-Distribution Cross-Docking: Items from various suppliers are received and sorted, then combined into mixed pallets to be shipped to distributors or customers.
- Retail Cross-Docking: Products from multiple vendors are sorted and sent directly to retail locations without long-term storage, enabling faster distribution to stores.
How Does Cross-Docking Work?
The goal of cross-docking is to minimize storage time while optimizing supply chain efficiency. This requires real-time coordination, often facilitated by automation and warehouse management system (WMS) software to ensure smooth transitions from inbound to outbound logistics. The process typically involves the following steps:
- Receiving: Inbound goods are delivered to the warehouse.
- Sorting: Products are sorted based on their destination or order.
- Processing: Goods are processed, consolidated, and prepared for shipping.
- Consolidating: Products are grouped and organized into outbound shipments.
- Shipping: Goods are dispatched to their final destination.
Benefits of Cross-Docking
When implemented effectively, cross-docking can significantly improve supply chain efficiency. Below are some of the key advantages:
- Reduced Storage Space: Since products are transferred quickly, cross-docking reduces the need for large storage areas, which helps cut warehouse and overhead costs.
- Lower Inventory Costs: Cross-docking minimizes the need for large inventory stocks, reducing capital tied up in unsold goods. It also helps reduce the risks of stock obsolescence, especially in industries with short product life cycles.
- Greater Supply Chain Efficiency: With products moving directly from suppliers to customers without delays, the supply chain becomes faster, leading to quicker deliveries and higher customer satisfaction.
- Reduced Product Handling: Less handling means fewer chances for damage and lower labor costs. It also shortens turnaround times, contributing to better overall efficiency.
- Sustainability: Cross-docking helps reduce transportation emissions and warehouse energy consumption by minimizing the need for storage and optimizing transportation routes.
Challenges of Cross-Docking
Despite its advantages, cross-docking is not without its challenges:
- Complex Coordination: The process requires careful planning and collaboration between suppliers, logistics teams, and transportation networks to ensure timely arrivals and departures.
- Infrastructure Investment: Setting up a cross-docking facility demands significant upfront investment in specialized layouts and technology to enable efficient sorting and quick turnover.
- Limited Product Suitability: Some products, particularly those requiring inspections or regulatory checks, may not be suitable for cross-docking due to the need for more stringent handling.
- Dependence on Reliable Suppliers: The effectiveness of cross-docking relies on suppliers’ ability to deliver goods on time and accurately. Any delay or error can disrupt the entire process.
- Advanced Technology Requirements: Efficient cross-docking requires advanced technology to manage real-time logistics and inventory data, which can be a barrier for companies without the necessary infrastructure.
Enhancing Your Supply Chain with Cross-Docking
Looking to implement cross-docking in your supply chain? Platforms like Extensiv can help you navigate the complexities of cross-docking by providing real-time inventory tracking and automation. With powerful warehouse management systems (WMS), Extensiv helps optimize sorting, processing, and shipping for 3PLs and eCommerce businesses, ensuring smooth, efficient operations.
Whether you’re managing in-house logistics or outsourcing fulfillment, Extensiv’s solutions integrate with your partners and clients for seamless collaboration. This leads to reduced costs, faster delivery times, and an overall more efficient supply chain.
Ready to streamline your supply chain and boost efficiency with cross-docking? Request a demo to discover how Extensiv can help make your logistics operations more effective.
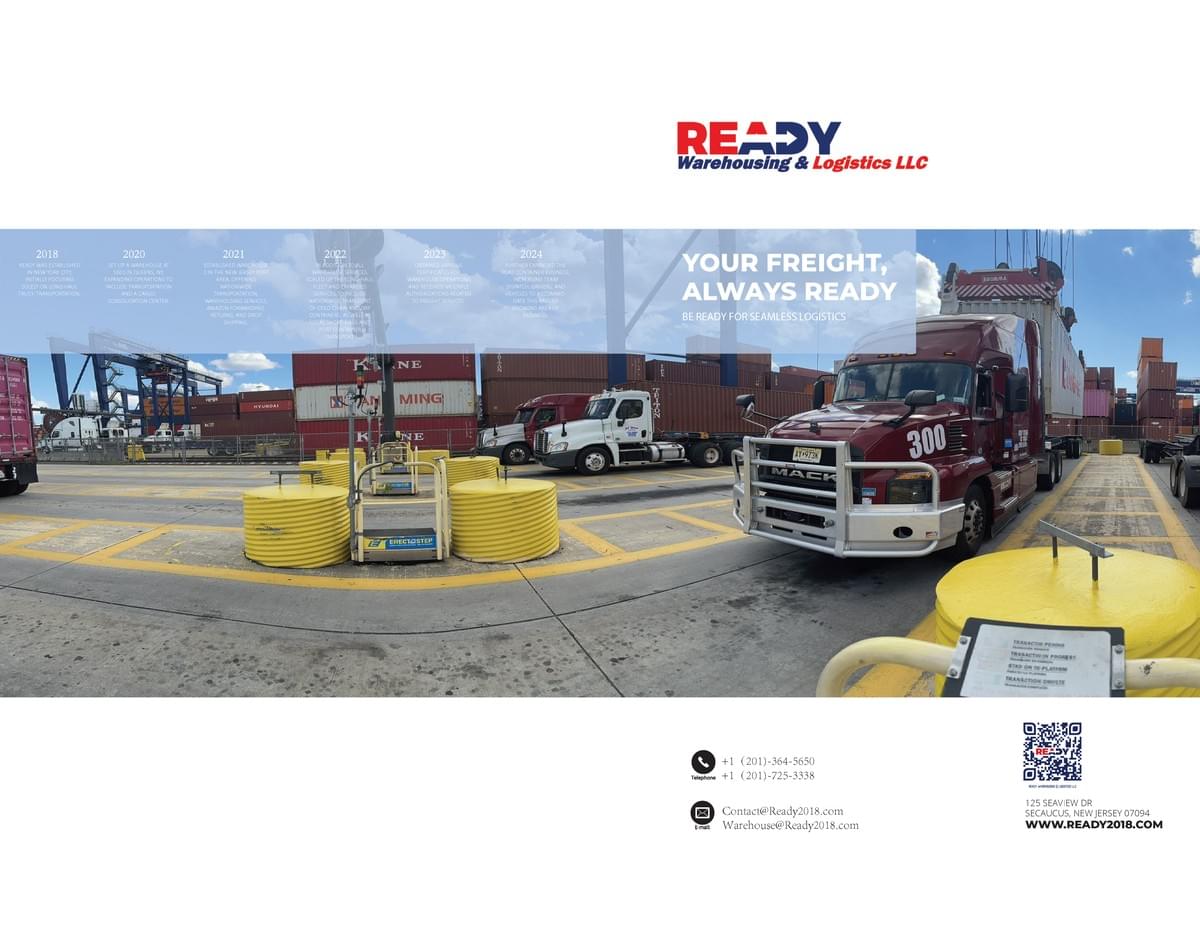